COLLECTION AND DRYING OF SARGASSUM
Sargassum is collected from beaches or the sea using existing market procedures, such as trucks, shovels, and tractors. Once collected, the seaweed undergoes the drying process using a conveyor belt machine with a stepped design. This machine acts as a tunnel with cylindrical parabolic solar heaters on its roof, which heat the thermal oil (PARATHERM) to temperatures of up to 330 degrees Celsius.
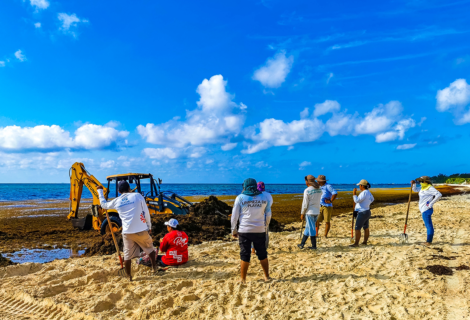
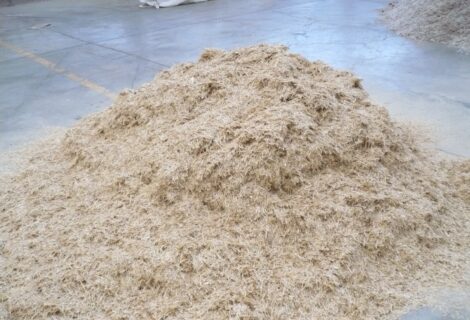
PROCESSING OF MDPE PLASTIC
The Medium-Density Polyethylene (MDPE) plastic, sourced from supermarket bags, packaging, and waste, is first densified with heat and then ground in the blade mill. It is subsequently combined with the dried and ground sargassum. This mixture is then fed into the molding machine to create synthetic wood sheets.
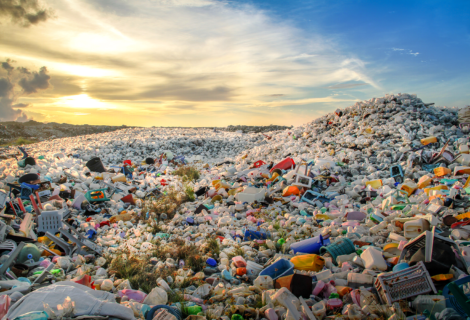
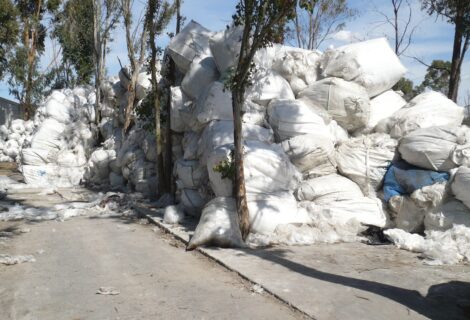
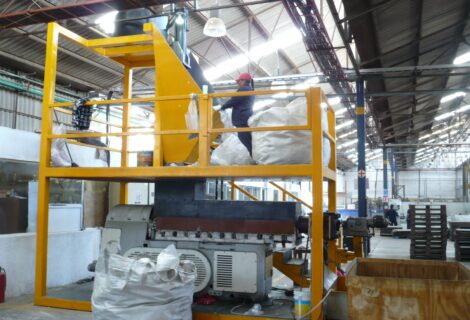
COOLING AND FINISHING
To prevent deformation of the sheet, it is essential to cool it simultaneously across its entire surface. For this purpose, the press, along with the mold, is submerged in a cold-water.
Subsequently, the sheet is dimensioned, the edges are cut, and it undergoes a sanding process to achieve the final finished product.
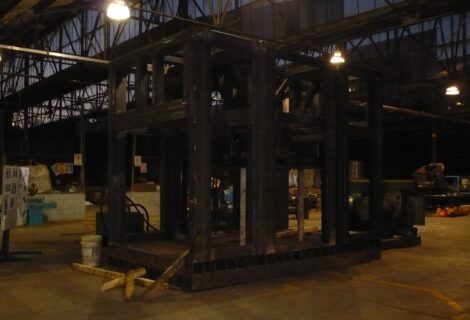
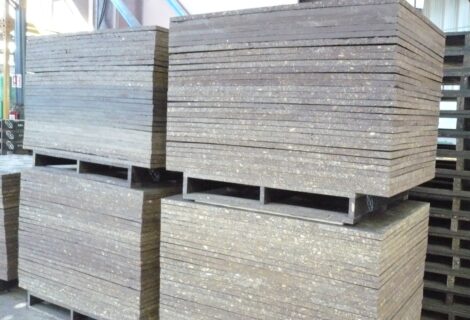
ELIMINATING CONTAMINANTS
Our procedure involves the fusion of MDPE plastic, which acts as a protective encapsulator for the ground sargassum particles, with a maximum size of 12 mm, and the thickness of the sargassum sheet. As the plastic polymer melts and solidifies, it encapsulates any heavy metal particles present in the sargassum, effectively trapping them within the matrix.
The environmental benefits of our process are twofold. Firstly, it provides a valuable industrial application for sargassum, effectively eliminating the presence of this seaweed from our beaches. Secondly, it repurposes and gives an industrial use to MDPE plastic waste from bottle caps, wrappers, and other medium-density polyethylene materials, preventing their decomposition or combustion in open air and reducing emissions of harmful substances like dioxins, methane, and CO2.
Additionally, impurities like grains of sand, composed of calcium carbonate (CO3CA), are often found in sargassum. These impurities are soft and inert, and during the fusion process, they become trapped within the polymer matrix as well.
0
PRODUCED
48 TONS
0
SARGASSUM
PROCESSED
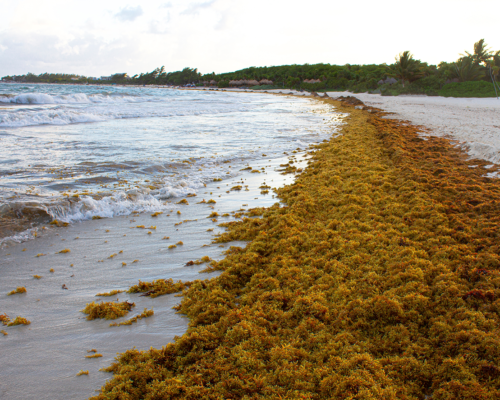
SARGASSUM PROCESSING CAPACITY
Our cutting-edge Sargassum Eco Lumber Manufacturing Machine is capable of processing an impressive amount of sargassum efficiently. In just 24 hours, this machine can produce a staggering 48 tons of 4 x 8 feet panels, with sargassum comprising 60% of the total weight. This translates to approximately 28,800 kilograms of sargassum processed daily by each machine.
However, the beauty of our solution lies in its scalability. If the demand for the final product, the eco lumber panels, surges, we have the flexibility to install additional machines. This means that we can scale up production to meet market demands and process even larger quantities of sargassum. By doing so, we not only contribute to environmental conservation but also cater to the growing demand for sustainable construction materials.
Our adaptable manufacturing process enables us to meet the needs of an environmentally-conscious market and contribute to building a more sustainable future.
OUR PROCESS: ENVIRONMENTALLY FRIENDLY AND SUSTAINABLE
In our commitment to environmental preservation, we take pride in our dry process, powered solely by solar heat with temperatures reaching up to 180 degrees Celsius. With zero reliance on fossil fuels or organic solvents, our production method ensures minimal ecological impact. Gone are the days of harmful emissions, as our process produces no dust, vapors, or smog, safeguarding the atmosphere and local air quality.
Our dedication to sustainability extends even further as we repurpose the MDPE plastic, a known pollutant, during our eco-friendly process. By transforming this plastic waste into premium-quality EcoLumber, we not only divert it from landfills but also contribute to reducing plastic pollution in oceans and natural habitats.